Setting sustainability targets, managing the process during the design stage, and then ensuring benefits are realized in practice (during operation) are three key sustainability requirements for many building refurbishment and fit-out projects.
This checklist includes energy & environmental design and development ideas that can be employed by fit-outs teams to contribute to the sustainability goals of their client organizations – and also to highlight and promote the good sustainability measures they are employing.
Follow the checklist ideas below to help reduce energy consumption and improve overall environmental impact of fit-out refurbishments to achieve the ‘Win Win’:To do this, this checklist draws on some fundamental themes:
- Design for best practice operational resources use (energy, water, waste) to contribute to the global commitment towards Net Zero and the development of zero carbon buildings.
- An ethical ethos for materials selection to reduce environmental impact on the planet and our communities.
- Benefits realization of the design intent into best practice operational performance; share your good practice measures and experiences so we can learn from each other.
A key driver for this is ensuring our fit-out and refurbishment projects meet best practice industry standards.
Benefits of using structured approaches to sustainable refurbishments
- 1Tap into well know environmental assessment tools for decision-making and target key sustainability criteria.
- 2Prioritize which measures to focus on and when (while giving flexibility to fit-out teams).
- 3Embed industry good practice and legal compliance; rank different project aspects based on impact.
- 4Enable performance reporting to stakeholders; enhance reputation and recognition.
- 5Track achievement by collating and referencing evidence; independent verification can be used if required.
The 25 opportunities below have been divided up across the Big Green Challenge 5-R categories. These are aligned with the good practice order of measures, focusing on measures first that are not only reduces demand but also right sizes subsequent investments in new systems and technology.
We hope this checklist sparks some new ideas for you!
REVIEW
The first step to take to improve understanding of the existing installation and set the strategic objectives for the development fit-out
1. Review existing operations and current levels of performance
- What do existing building users think about the different aspects of their working environment? What are their main frustrations? What ideas do they have for improvements?
- Understand the outcome requirements of the building and the processes involved. What are the needs and expectations of the key stakeholders?
- Analyze past and current energy and utilities use. Identify the significant consumers and any relevant variables that impact on consumption. Talk to stakeholders who can impact on the performance of these significant consumers.
- Consider ideas and opportunities to improve sustainability performance.
![review_1-min[1]](https://biggreenacademy.com/wp-content/uploads/2020/10/review_1-min1-e1602513390742.jpg)
2. Understand the latest legislation and standards requirements for the project
- Ensure you’re up to date and complying with all relevant and local environmental legislation and building standards – for example, check for the latest application local building regulations and any standards applied by the client organization.
- Check with specialist process suppliers about any other specific legal requirements.
- Determine how these requirements apply to the project’s overall environmental & sustainability performance.
- Understand the relevant strategic risks, opportunities and priorities of the organization and the business processes to be refurbished. Look for ways to support other management objectives in a way that’s a Win for All.
- Communicate the importance of effective energy & sustainability management and of conforming with environmental design criteria. Promote the importance of the continual improvement philosophies of international best practice standards.
- Ensure the appropriate procedures are established and implemented to embed sustainability practices with the design and fit-out program.
- Ensure the responsibilities and authorities for relevant key roles are assigned and communicated within the project and the organization.
3. Agree and set sustainability objectives and targets for the project
![review_3-min[1]](https://biggreenacademy.com/wp-content/uploads/2020/10/review_3-min1-e1602513515311.jpg)
4. Tap into well-know environmental assessment tools for decision making about overall sustainability performance
- Use an environmental criteria based scoring method to facilitate discussions about which measures to target at concept design stage.
- Among the globally recognized criteria assessment approaches, BREEAM and LEAD are the most recognized, both of which apply to development and refurbishment.
- The Ska Rating scheme, originally developed by Sweden firm Skansen, is an example scheme that specifically applies to fit-outs. It uses a free on-line tool this can take into account different project scales, size and budgets. The project is scored based on relevant ‘measures in scope’, usually between 30 and 60 measures depending on the complexity of the project.
- Whichever scheme you choose, you want one that utilizes life cycle analysis to weight different sustainability measures to optimize overall performance.
5. Define the overall level of sustainability practice you are looking for from the fit-out or refurbishment
- A Ska Rating requirement, for example, can be set at Bronze, Silver or Gold levels for overall environmental sustainability practice:
- Gold level is for score 75% or above – this is a good level for strong teams with experience of Ska measures, and where broad best practice environmental sustainability requirements and an engaged supply chain apply
- Silver is for score of 50% to 75% - good for teams with some experience of Ska and where sustainability requirements look to push boundaries in core areas and good relationships within supply chains apply
- Bronze is for score of 25% to 50% - for teams new to Ska and where sustainability requirements focus is just beyond compliance
- Agree target levels early on for any project. As part of the process, you can make certain (Ska) measures compulsory so they must be targeted by the fit-out team.
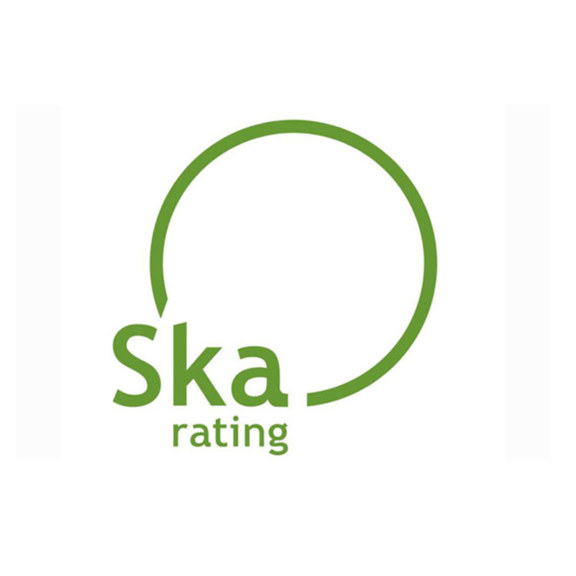
REDUCE
First target improvement measures that directly reduce the energy & environmental impact of the operation concerned
1. Target metered operational energy consumption
- This should be a requirement for any project, which includes significant upgrades, new energy consuming equipment or building services systems such as lighting, ventilation, and air-conditioning.
- Reduction targets should be set against operational energy base-lines, based either on current consumption of the metered zone or similar related benchmarks.
- Targets should ideally be set in specific energy terms, for example, in kWh per m2 of space. You may agree on a minimum target, with a view that this is a minimum level to be exceeded as much as possible. We usually apply a minimum reduction target level of 10% for the refurbishment projects we’re involved with.
- Progress towards the target levels should be periodically reviewed over the project. For a rolling program of similar refurbishments, these targets should also be reviewed with a view of tightening them over time as experience grows.
![reduce_1-min[1]](https://biggreenacademy.com/wp-content/uploads/2020/10/reduce_1-min1-e1602513640564.jpg)
2. Provide a forecast for metered energy consumption in operation
- The forecast should be in absolute annual consumption terms, for both metered units (e.g. kWh) and cost in local currency.
- We often specify the use of a simple energy assessment method, using an Excel spreadsheet template, that schedules out all energy users for the space, and estimates consumption based on expected operation profiles and utilization and load factors (based on experience).
- We find that this can be used by design teams to facilitate design discussions with eventual building users.
- More sophisticated methods exist to develop forecasts, for example using dynamic simulation energy models.
- Actual operational energy consumption in use will also depend on operational practices and user behaviors.
3. Target metered operational water consumption
- This should be a requirement for all fit-out and refurbishment projects involving installation of any systems or equipment that are likely to lead to significant water consumption.
- Setting consumption reduction targets and forecasting metered water consumption in operation can be more difficult for water performance – do this if you have good experience in understanding water consumption for the application at hand.
- Alternatively, to meet best practice water performance specifications, we can focus on achieving maximum flow rates specified for individual significant water consumers within environmental assessment criteria.
- For example, BREEAM New construction Wat 01 table defines maximum permissible water flow rates for significant water consumers. To meet level 3 performance specification, for example, would require all general taps to limit water flow rate to less than 4.5 liters of water per minute, showers restricted to < 6 liters/minute etc.
- If possible, at the very least, specify the generation of an (approximate) metered water forecast to help better understand impacts on operational absolute annual consumption (liters) and cost (in local currency).
![reduce_3-min[1]](https://biggreenacademy.com/wp-content/uploads/2020/10/reduce_3-min1-e1602514135673.jpg)
4. Target ethical materials selection to reduce environmental impact
- This should be a requirement for all fit-out and refurbishment projects involving procurement/installation/disposal of any wood panels, joinery, timber structures and flooring, furniture, particle boards, paper products, textile and laminated floor coverings, wall coverings, furniture and soft furnishings, and ceiling tiles.
- Timber is usually an easier one to target. For example, you can specify 100% timber to be either reclaimed, recycled or, when new, to be supplied with a chain of custody certificate from one of the following forest certification schemes only: FSC, PEFC, SFI, CSA.
- For other materials selection, if possible: avoid the use of any products containing PVC; design to minimize the use of virgin plastic products and packaging; all paints, wall coverings and adhesives to have low or zero VOC emissions (identified by a certified low VOC emissions label).
- All wood panels, joinery, timber structures and flooring, textile and laminated floor coverings, wall coverings, furniture and soft furnishings, and ceiling tiles contain zero or low formaldehyde content (identified by a certified low VOC emissions label).
- See our guide to eco-labelling for materials selection.
5. Target waste processes to minimize impact
- This should be a requirement for all fit-out and refurbishment projects involving disposal of any products, systems, equipment or packaging.
- Target opportunities to design out waste and record design solutions to reduce materials consumption and wastage during construction and once the refurbished space is in use.
- Prepare a site waste management plan (SWMP) and target a high level (usually 90%) of waste produced from the fit-out/refurbishment activities diverted from landfill.
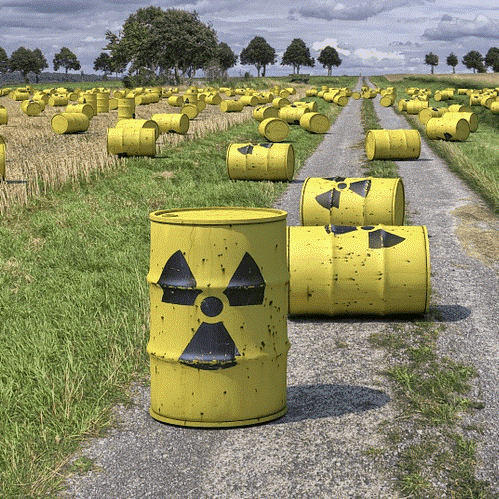
REUSE
Once environment impact measures have been specified, then ensure
1. Track overall sustainability performance during project progress.
- Detailed design signoff is often a key checkpoint for examination of performance. It is usually good practice for a project sustainability champion to coordinate by the design team’s response to performance requirements. The design team can use a sustainability statement, along with its evidence pack, to demonstrate the response to the agreed sustainability targets in scope.
- This would include confirmation that the design meets or surpasses the agreed Ska Rating target (or other assessment target, as used). This can be demonstrated by using the online detailed design Ska report and associated evidence and references pack.
- Where any requirements cannot be met, this statement can be used to make the relevant justifications. These should be agreed by the client at the earliest opportunity, and prior to any procurement or construction activity.
- It would be expected that any specific sustainability requirements are included in all preliminaries/tender documents. There should also be confirmation, for example, that continuation of a Ska assessment is specified for the construction process used by the contractors, as required. The online Ska project can hold all the evidence and document references required for all measures targeted during design and construction stages.
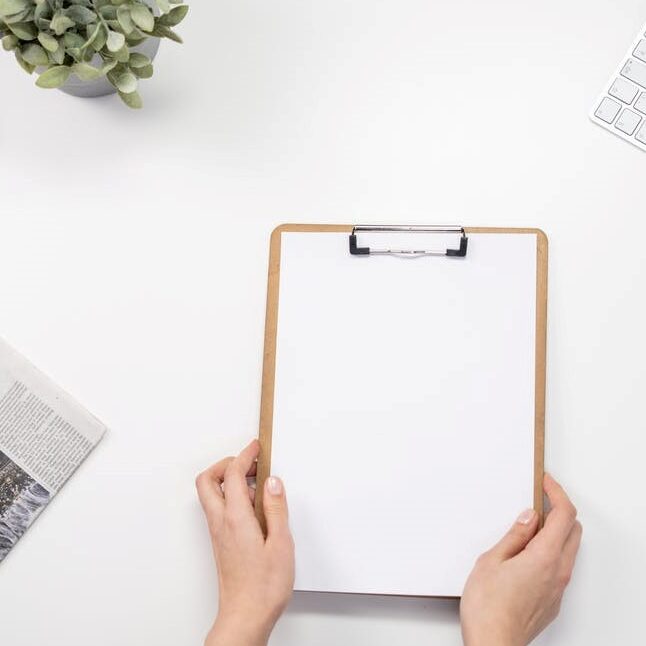
2. Confirm metered operational energy consumption targets are met.
- When in scope, we would normally expect a statement that confirms the refurbishment meets or surpasses the agreed design energy target, as shown in an appended energy forecast model undertaken by a competent person. This should include detail on the energy performance benchmarks and baselines used and how they were derived, e.g. including the period of any data used (normally 12 months).
- Include a list/description of the good practice energy efficiency measures used in the design, including technical and other measures to facilitate operational/behavioral controls. Include commentary on control equipment and operational controls, for example on your zoning strategy, temperature controls, demand controls, lighting dimming controls, display lighting and other time controls, etc. See Ska best practice measures for guidance.
- Baselines can be adjusted for changes in expected business activity, if there is a demonstrable statistical correlation between business activity and energy consumption.
3. Confirm metered operational water consumption targets are met
- When in scope, we would normally expect a statement that includes a conformation statement that the flow rates for all individual components to be used meet, or are lower than, the specified standard (e.g. level 3 flow rates defined by the latest version of BREEAM New construction Wat 01). This would be demonstrated on a water consumer schedule compiled by a competent person.
- Include an (approximate) forecast of metered annual water consumption in use (liters) and cost (in local currency).
- Include a list/description of the good practice water efficiency measures employed in the design to minimize operational water use.
![BREEAM-min[1]](https://biggreenacademy.com/wp-content/uploads/2020/10/BREEAM-min1-e1602513680856.jpg)
4. Confirm ethical materials selection is being met
- When in scope, we would normally expect a statement that provides assurance that all materials meet the project’s specific materials requirements.
- Justification for the material selection not meeting these requirements can be made in reference of the reasons for the product used (e.g. based on H&S, hygiene requirements or other ethical reasons) that demonstrates that a market review of alternative products has been carried out, as appropriate.
- If possible, select products that use third-party verification labels/certification, recycled content, environmental product declarations etc. to ascertain sustainability credentials.
- Try using PVC free from Phthalate and Cadmium, that contain post-consumer recycled content, and that achieves 100% recyclable status (i.e. designed for deconstruction to enable recyclability), or demonstrate that it is a more favorable product than alternatives through, for example, a Life Cycle Analysis. A scheme such as the BRE Green Guide to Specification or Green Book Live database can be used to demonstrate a good rating in life cycle impact terms.
- Avoid the use of virgin plastic products and packaging. Source sustainable natural materials instead of plastics, or source 100% recyclable plastics with a high recycled content (i.e. designed for deconstruction to enable recyclability).
- Include a list of all products with medium or high VOC, or formaldehyde emissions levels that do not meet industry label or certification standards. Remember to check formaldehyde content of furnishing, carpets, fabric seating and textile wall coverings to ensure they are E0 or E1.
- There is a global push to prioritize non-HFC refrigerants with low global warming potential. Consider all available technical features and specifications employed to minimize the use of HFC refrigerants in fit-outs, including considering other options, such as CO2 systems, if available and practical.
5. Confirm waste processing targets have been met
- We would normally expect a statement that details the key measures taken on: how possible waste is being designed out (e.g. take back scheme for packaging waste), the use of reusable packaging, designing out waste in design stage; optimizing prefabrication, effective storage of materials to reduce waste etc.
- Include detail, if appropriate, on how a pre-construction site waste management plan (SWMP) will be used to minimize avoidable waste.
- Provide the pre-construction SWMP to the client organization with targets for resource efficiency (e.g. in tons) and percentage of waste diverted from landfill.
![reuse_5-min[1]](https://biggreenacademy.com/wp-content/uploads/2020/10/reuse_5-min1-e1602514189605.jpg)
RECYCLE
Talk to colleagues, share experiences and communicate the design intent to operators
1. Ensure you’re ready for handover to building users and operators
- Is the benefits realization plan for ensuring environmental performance in operation realistic and achievable?
- Have you defended strategic requirements against changes in handover plans? Are there any knock on effects from changes in any internal or external events?
- Has full user and system testing been done to your satisfaction so you can go live? Are all the legal/other approvals in place?
- Is the organization ready, willing and able to take control, with the necessary resources, skills and contracts in place?
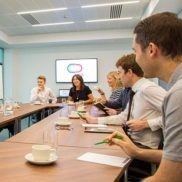
2. Set handover plans and compile project handover documents
- Communicate the design intent to building owners/operators so they understand the principle sustainability strategies and practices in use. Include the evidence demonstrating that targets and key requirements have been met. Provide principle contact details for sustainability performance from the design team.
- Define building commissioning and handover processes required for optimum performance, detailing requirements, and agreed responsibilities.
- Communicate requirements for ongoing maintenance, any post occupancy evaluations, aftercare contracts, measurement and verification processes for performance levels.
- Include post project reviews to assess and capture benefits achieved to implement in future projects. Performance in use reviews would normally wait until after one year of operation to establish effectively how well the fit-out has performed against its design targets.
3. Share the key environmental assessment reports and (final) energy and water use forecasts
- Share a copy of the final project sustainability statement. This should be applicable for the final as-built development and drawings.
- Download the Ska (or equivalent) post-construction completion report, which demonstrates the Ska rating achieved, and lists all the good practice measures targeted with accompanying evidence pack.
- Detail the absolute forecasts expected for annual metered energy and water consumption – use them to set budgets and targets for the first period of operation.
- Include the plan to review actual versus expected energy/water consumption in operation, and how to feed back the resulting performance to the refurbishment team.
![recycle_3-min[1]](https://biggreenacademy.com/wp-content/uploads/2020/10/recycle_3-min1-e1602514261239.jpg)
4. Feed into environmental management practices required in operation
- Detail energy, water and waste management practices to be included in an operation manual; include opportunities for conservation measures and, for example, recycling of food and other waste streams.
- Produce agreed handover documents e.g. a building logbook and/or a non-technical user guide.
- Support activity to raise awareness of project sustainability features and operation methods to colleagues and building users
- Include the plan for driving continual improvement in future performance.
5. Compile a summary case-study of key sustainability ‘wow’ factors
- This would normally be a summary of the strategic requirements, project objectives, the key measures taken and the outcome results.
- If possible, include learnings you can share that may help others deliver and demonstrate better sustainability performance within future projects.
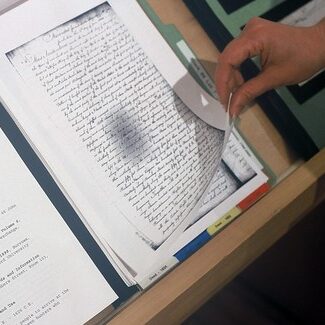
RETHINK
Challenge mindsets, rethink for operational opportunities for continual improvement, trial ideas and roll-out what works best
1. Work with the organization to help bring together the vision, strategies and policies for better sustainability in operation
- Demonstrate and reconfirm how the refurbishment strategies will deliver better environmental performance and continual improvement, contributing and aligned to the organization’s overall purpose, priorities and values.
- Reconsider whether the vision for better performance is inspiring enough to harness colleague’s hearts and minds in operation. Discuss with key stakeholders as appropriate.
- Review (to reset) environmental sustainability policies focused on delivering the operational outcomes required. Redefine the relevant strategic metrics and targets against key organizational priorities/stakeholder groups.
- Make recommendations for the environmental performance accountability strategy – this will depend on project and operational scale and complexity.
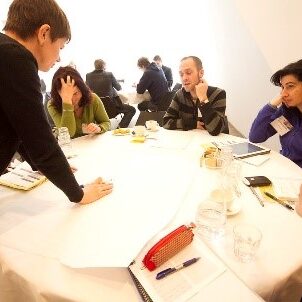
2. Consider a principal role for overall accountability for environmental performance.
- Rethink how operational strategies can offer oversight and accountability for end-to-end coordination and operational outcomes across all business processes.
- Often need adequate competency and authority in environmental leadership and ability to communicate well across organizational teams.
- Responsibilities may include: asking for building user feedback to assess levels of service achieved, considering future changes in use, assisting with fine tuning building services and operational systems, reviewing building management system controls (and fine tuning performance in each season), updating manuals and records to reflect any changes, comparing energy consumption on sub-meters against targets/simulated forecasts, feeding back lessons learnt from post occupancy reviews, etc.
3. Agree tough but fair operational resource performance targets in use
- Focus on metered utilities consumption; include both regulated and non-regulated consumption if distinction is made within local building regulations.
- Keep it simple, and focus on getting the basics right to deliver best value across the range of organization’s priorities while embracing collaboration, innovation and – if needed – a culture shift.
- Base targets on realistic operational profiles to review and reset consumption forecast models. Accurate forecasts usually rely on good information on utilization and load factors of equipment in use. Don’t worry if forecast consumptions are based on crude estimates – the important thing is to start the process.
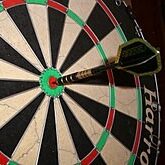
4. Regularly report on progress and overall environmental performance
- Put in place monitoring, measurement and analysis processes to evaluate and report on progress and performance, e.g. using monthly dashboards. Remember to show clear line of sight to delivering the organizational strategic operational outcomes.
- Include tracking of energy, water and waste performance and actions taken.
- Include ongoing compliance status with local legal and other environmental requirements. Regularly review and update the applicable legal and other requirements.
- When possible, feedback performance to the refurbishment design team.
5. Drive continual improvement in environmental performance in use
- Top management should habitually review environmental performance and control checkpoints to ensure their continuing suitability, effectiveness and alignment with the strategic direction of the organization.
- Collaborate with operational colleagues, service partners and other significant building users to review and drive ways to achieve continual improvement in overall environmental performance. Include training as necessary.
- If automatic building management control systems are used, makes checks for consistency between actual control settings and control strategies used and the intended descriptions of operations (‘Desops’) and continually develop and refine them as necessary.
![rethink_5-min[1]](https://biggreenacademy.com/wp-content/uploads/2020/10/rethink_5-min1-e1602514552766.jpg)
SUMMARY
A building refurbishment or fit-out is a great moment of opportunity to make changes to significantly improve the environmental performance of buildings and operations.
We find that following the 5-R categories helps ensure the remedial measures are considered in an order that are not only ensure lowest overall investment cost (for refurbishment/fit out) but that also right sizes subsequent investments in technology.
Download
If you would like a downloadable summary checklist for this, please contact us.
- It’s in Microsoft Word, but it can easily be converted to another Word processer, such as Google Docs. It’s read-only, so you’ll have to save your version onto your own drive to be able to modify it.
- You can then modify and develop this simplified checklist to suit your needs as required. Complete it on line or print it out (but remember: think before you print!)
For more detail about developing an approach to optimizing the energy performance of process systems, check out ISO 14001 and other related standards.
Written by James Brittain and Beverley Lister